Optimizing the Cost of a Float Glass Production Line
The production process of float glass is both intricate and costly, demanding meticulous management to ensure efficiency and cost-effectiveness. This article delves into the critical aspects that contribute to the overall expenditure in a float glass production line, offering insights on optimization strategies for economic viability.
Initially, it's essential to understand that the cost of a float glass production line encompasses various elements including raw materials, energy consumption, machinery depreciation, labor expenses, and maintenance protocols. The high temperatures required for melting sand, soda ash, and other ingredients into molten glass consume a significant portion of the operational budget due to the sheer amount of energy necessary.
Machinery plays a central role in determining production costs. Advanced technology can reduce energy usage and increase output, but comes with higher initial investment and maintenance fees. Balancing the trade-off between upfront costs and long-term savings is crucial. For instance, investing in energy-efficient furnaces can lead to substantial savings over years of operation.
Labor represents another considerable expense, necessitating a skilled workforce capable of managing the complexities of the production process. Automation can mitigate some of these costs by reducing the need for manual intervention, yet it requires substantial capital outlay and ongoing software updates and hardware maintenance Automation can mitigate some of these costs by reducing the need for manual intervention, yet it requires substantial capital outlay and ongoing software updates and hardware maintenance
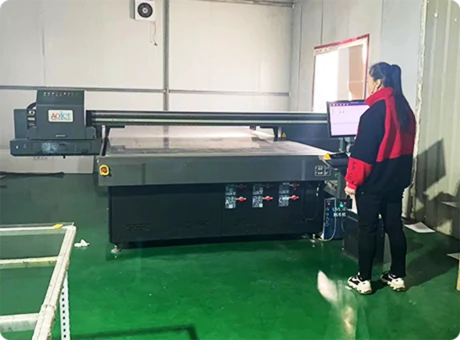
Automation can mitigate some of these costs by reducing the need for manual intervention, yet it requires substantial capital outlay and ongoing software updates and hardware maintenance Automation can mitigate some of these costs by reducing the need for manual intervention, yet it requires substantial capital outlay and ongoing software updates and hardware maintenance
float glass production line cost.
Moreover, the production line's throughput capacity and efficiency are directly correlated to cost effectiveness. Higher throughput allows for economies of scale, spreading fixed costs over more units of production. Efficiency improvements such as reducing waste and downtime also play a vital role in cost reduction.
Maintenance is often underestimated in its contribution to the production line's financial health. Regular inspections and prompt repairs prevent costly breakdowns and preserve the lifespan of equipment, ultimately saving on replacement costs.
In conclusion, optimizing the cost of a float glass production line involves comprehensive analysis and strategic planning across various dimensions. From embracing energy-efficient technologies and enhancing automation to improving worker skills and implementing rigorous maintenance schedules, each facet contributes to the delicate balance of quality and cost-efficiency in float glass manufacturing.