Float glass production is an innovative and highly technical process that plays a vital role in modern architecture, automotive industry, and various other sectors. This method was first introduced in the early 20th century and has since revolutionized the glass manufacturing industry.
The float glass process begins with raw materials, primarily silica sand, soda ash, limestone, and recycled glass. These ingredients are accurately measured and mixed together in a melting furnace, where they are heated to temperatures exceeding 1700°C. This intense heat transforms the mixture into molten glass.
Once the molten glass reaches the desired consistency, it is then poured onto a bed of molten tin in a continuous ribbon. The use of tin as a float surface is critical due to its low chemical reactivity, ensuring the glass remains uncontaminated. As the glass floats on the tin, it spreads evenly and cools slowly, giving it an unparalleled optical clarity and flatness. This step is the essence of the float glass technique, differentiating it from other glass manufacturing methods.
After cooling, the glass ribbon is gradually solidified and transferred to annealing lehrs. Here, it undergoes a controlled cooling process to relieve internal stresses and make it more durable Here, it undergoes a controlled cooling process to relieve internal stresses and make it more durable
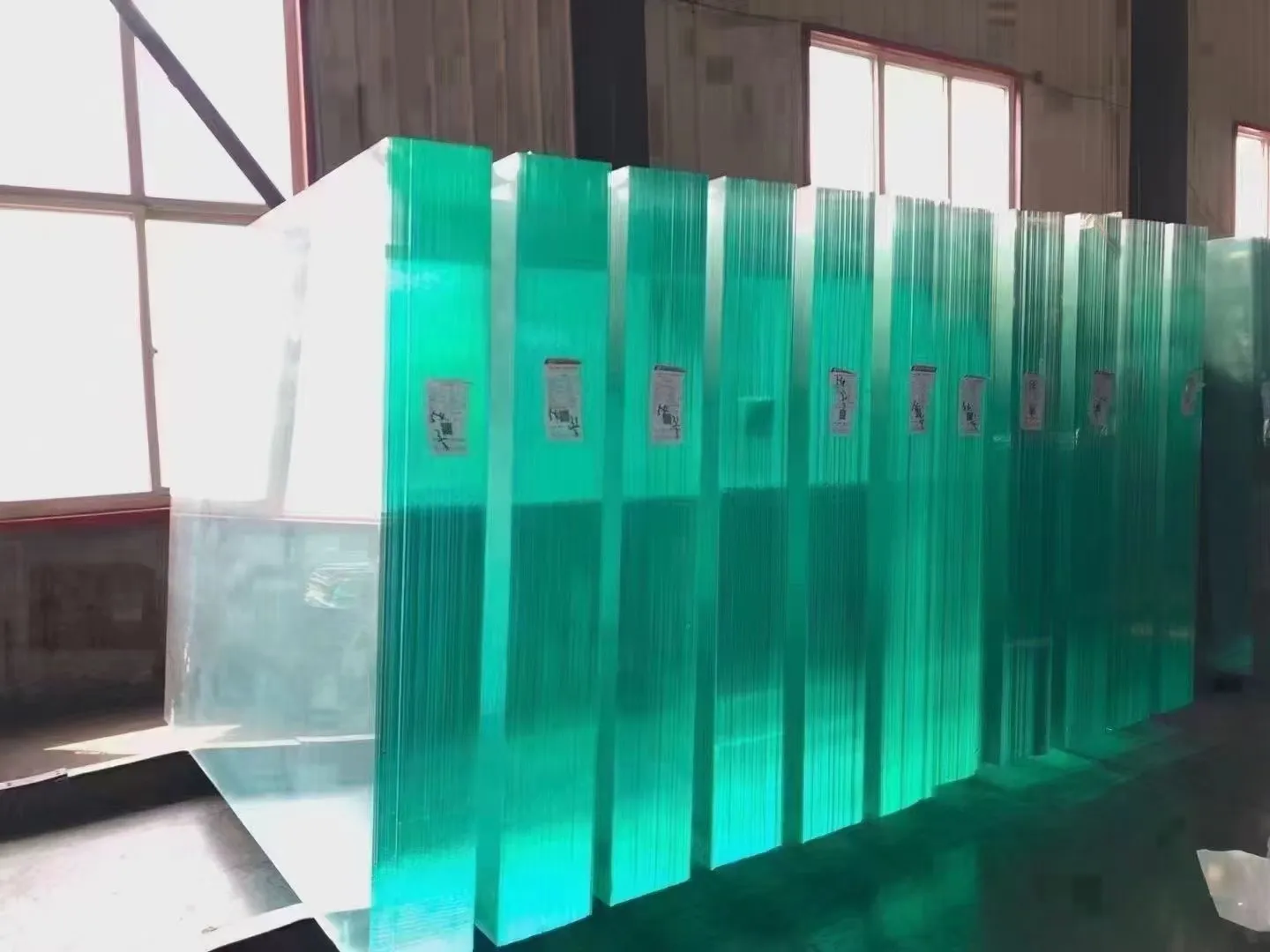
Here, it undergoes a controlled cooling process to relieve internal stresses and make it more durable Here, it undergoes a controlled cooling process to relieve internal stresses and make it more durable
float glass production. The glass then moves through cutting machines, where it is cut to the required sizes and shapes for various applications.
Float glass production is not only known for its high-quality output but also for its efficiency. The process allows for large-scale production, reducing waste and increasing productivity. Moreover, the uniformity and thickness control achieved through this method make float glass ideal for energy-efficient windows, mirrors, and architectural designs.
In recent years, the float glass industry has seen advancements in sustainability, with efforts to reduce energy consumption and emissions. Producers are investing in technologies to recycle waste glass and harness renewable energy sources, making the process even more eco-friendly.
In conclusion, float glass production is a testament to human innovation and engineering prowess. Its ability to produce large quantities of high-quality, optically perfect glass has made it indispensable in numerous industries. As technology continues to evolve, the future of float glass production promises further improvements in efficiency, sustainability, and product versatility.