The manufacture of tempered glass is a sophisticated process that has become paramount in our modern world, where safety, durability, and aesthetic presentation often go hand-in-hand. As an expert manufacturer within the glass industry, we delve into the complexities and nuances of tempered glass production to deliver unparalleled quality. Tempered glass, renowned for its strength and safety features, is a vital component in various industries, including construction, automotive, and consumer electronics.
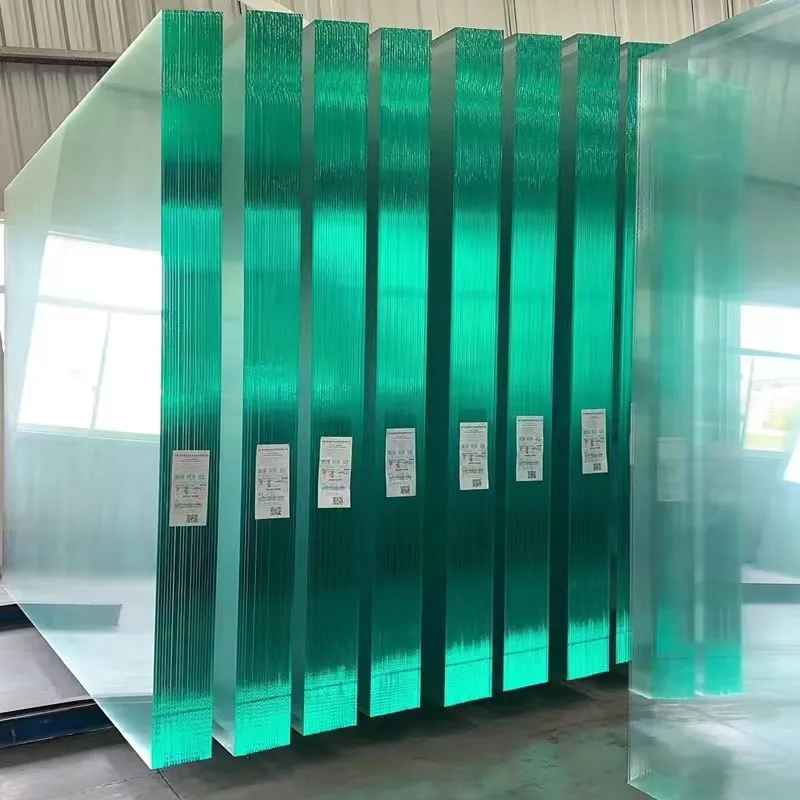
The journey of creating tempered glass begins with the selection of high-quality raw materials. Superior-grade silica sand, soda ash, and limestone are meticulously chosen to ensure glass clarity and integrity. Upon procurement, these constituents undergo rigorous inspection and testing in our state-of-the-art facilities to certify alignment with industry standards. Each batch of raw material is scrutinized for purity, chemical composition, and grain size, setting the stage for the formulation of pristine glass panels.
Commencing the transformation process, the raw materials are conveyed to the melting furnace, where temperatures soar to approximately 1,700 degrees Celsius. It's here that the materials fuse into a translucent liquid. Our engineers leverage advanced furnace technology to maintain uniform temperature distribution, ensuring homogeneous melting that leads to defect-free glass sheets. After this transformative phase, the molten glass is precisely cooled on controlled rollers to achieve the desired thickness, guided by specifications unique to each application.
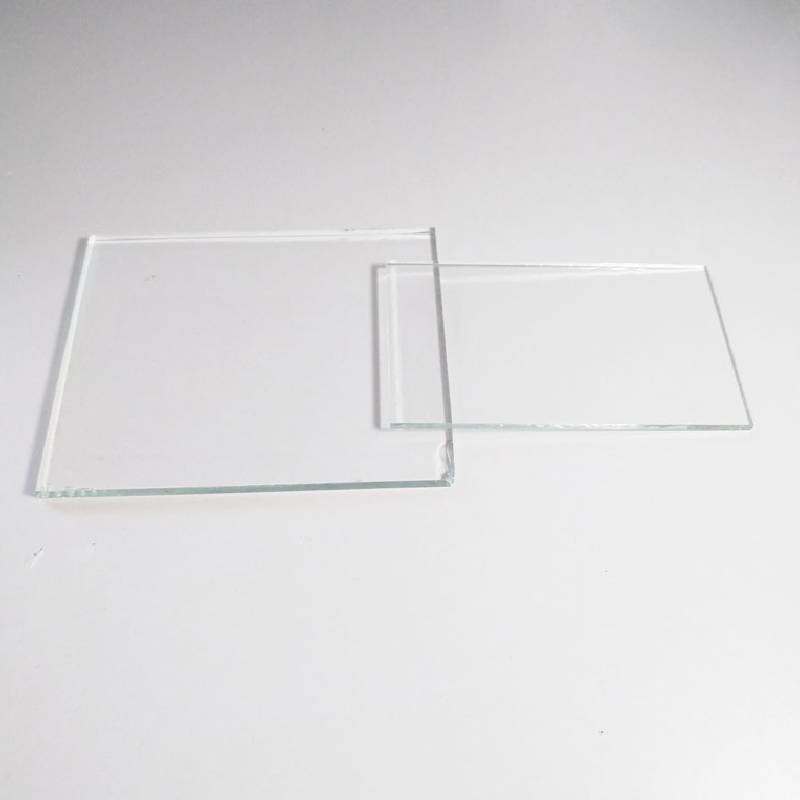
Once the glass has attained its preliminary form, it is subjected to meticulous cutting and edging operations. This is where our expertise shines. Precision instruments cut and shape each glass piece, minimizing chipping and surface damage. The importance of clean finishes is critical as even minor deviations or flaws can compromise the subsequent tempering process.
tempered glass manufacture
Tempering is where the glass undergoes its most significant metamorphosis. The cut glass, now known as float glass, enters a tempering oven where it is heated to over 600 degrees Celsius and then rapidly cooled through a sophisticated high-pressure airflow system. This stage imbues the glass with its characteristic strength — making it up to five times stronger than conventional glass. Additionally, the controlled cooling imparts compressive stress surfaces while ensuring tensile stress within the core. This unique stress profile not only enhances mechanical strength but ensures the glass shatters into small, blunt pieces if broken, mitigating injury risks.
A key element of our innovative process is quality control. Each pane undergoes rigorous inspection, both manually and through automated systems, ensuring that dimensions, flatness, and surface quality meet stringent guidelines. Our quality assurance protocols are derived from decades of industry experience and align with international safety standards, cementing trust in our final product. Special emphasis is placed on strength tests through mechanical and thermal shock assessments, ensuring the glass withstands real-world applications.
Our authoritative stance in tempered glass manufacture extends beyond mere production — it encompasses sustainable practices, too. By investing in eco-friendly technologies and processes, our operation minimizes its environmental footprint. Waste glass is recycled, and energy consumption is significantly reduced through heat recovery systems, demonstrating a commitment to sustainable development.
In conclusion, the manufacture of tempered glass at our facility is underpinned by an unwavering dedication to precision, quality, and sustainability. Through a harmonious blend of expertise, advanced technology, and rigorous quality control, we consistently deliver a product that exceeds customer expectations and upholds safety standards across diverse applications. Our tempered glass is not just a product; it is a testament to our relentless pursuit of excellence and our commitment to fostering a future that's as transparent and resilient as the glass we create.