Tempered glass, a cornerstone of modern construction and product manufacturing, stands out due to its enhanced strength and safety features. The process of creating this durable material is both a science and an art, refined over decades to meet the stringent demands of today’s technology-driven industries. This article unveils the intricate process behind tempered glass creation, shedding light on why it remains unmatched in reliability and appeal.

The journey begins with the selection of raw materials. High-quality silica sand is the primary component, chosen for its purity and availability. The sand is melted at extremely high temperatures, forming a molten glass batch. This requires precise temperature control, often exceeding 1700 degrees Celsius, to ensure uniformity and clarity. The expertise in this initial stage is crucial, as any impurities can compromise the integrity of the final product.
As the molten glass is carefully shaped into sheets, attention turns to cooling – a process integral to tempering. Rapid air cooling, known as quenching, is applied. Here lies the essence of tempered glass the outer surfaces cool quicker than the center, putting them under compression and the interior under tension.
This differential cooling is the secret behind the strength of tempered glass. Not only does this make it four to five times stronger than regular untreated glass, but it also ensures that, if broken, it shatters into small, blunt pieces rather than sharp shards, minimizing injury risk.
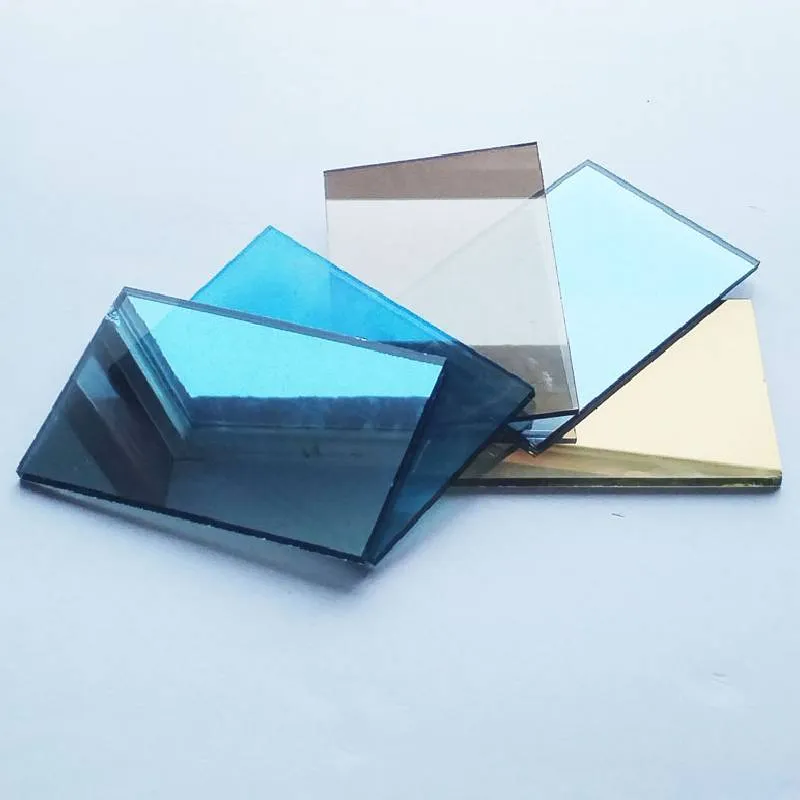
Expert craftsmanship is pivotal in this phase. Technicians must possess a deep understanding of thermal dynamics and mechanical properties. Using sophisticated machinery, they manipulate the cooling process, ensuring the correct balance between the glass's tensile and compressive forces. This manipulation is not just about safety but also about maintaining the glass's aesthetic qualities, crucial for architectural and decorative uses.
Beyond standard processes, modern advancements have introduced specialized tempering techniques tailored for unique applications. For instance, heat-soak tests are conducted to detect and address any inclusions like nickel sulfide that might cause spontaneous fractures. Such expertise assures quality and longevity, critical factors in constructing skyscrapers or manufacturing vehicles where safety and durability are paramount.
process of making tempered glass
In industries where even greater precision is required, such as electronics and optics, additional chemical tempering steps may be used. This involves immersing glass in a potassium salt bath at high temperatures to further enhance its strength and scratch resistance. This method, though more complex, offers an authoritative solution for products like smartphone screens, where everyday wear can compromise lesser materials.
Trustworthiness in tempered glass stems not only from its engineering but also from rigorous regulatory standards. Quality assurance testing under international benchmarks like those from ASTM and ANSI ensures that each batch meets specified impact resistance and temperature criterion. Compliance with these standards is non-negotiable, forming a crucial part of the production process that buyers and consumers depend on for safety and reliability.
Sustainability considerations have also become integral. Responsible manufacturers are now incorporating recycled glass, or cullet, reducing the ecological footprint of production. This shift not only enhances a company's authoritative stance in environmental stewardship but also resonates with eco-conscious consumers choosing products aligned with sustainable practices.
The seasoned expertise in producing tempered glass is reflected in its vast applications—from towering buildings and automotive innovations to everyday consumer electronics. Its trusted profile, built on a foundation of precise scientific processes, positions tempered glass as indispensable in today’s advanced industries. With continuous advancements in technology and sustainability, the future of tempered glass remains bright, promising even more robust, efficient, and eco-friendly solutions.
In conclusion, the process of making tempered glass is a testament to the blend of experience, expertise, authoritativeness, and trust that defines modern manufacturing excellence. As industries evolve, so does the glass, pushed to new limits and finding novel applications that enrich our lives and safeguard our spaces.